Technology
Technology
We have the key technologies needed to automate work sites—and we’re equipped with the flexibility to handle the unexpected challenges that come with real-world conditions.
What We Focus On
We support automation and digital transformation at work sites that rely on heavy machinery, such as construction sites, civil engineering projects, steelworks, mining operations, and cement plants.
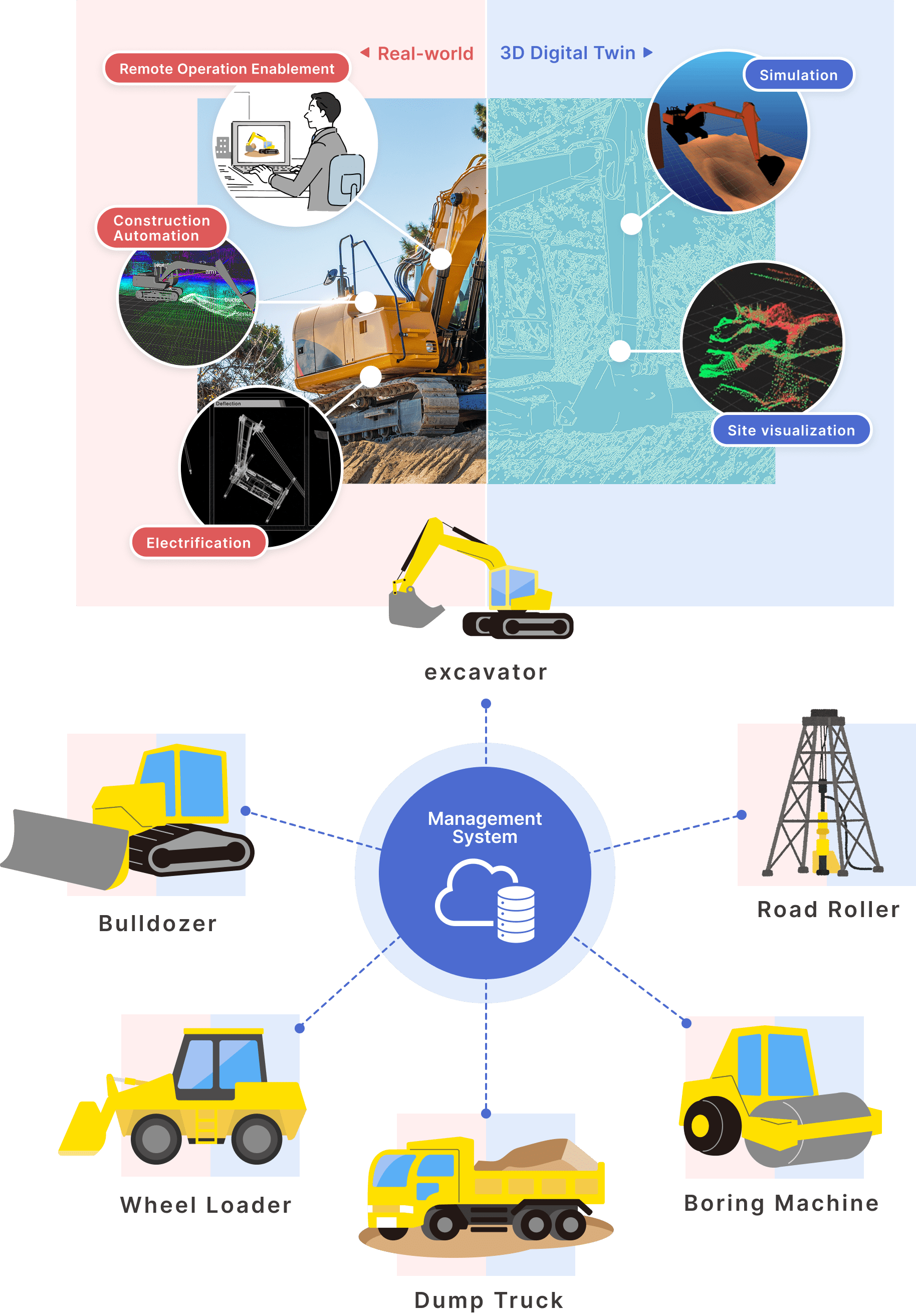
Flexible System Architecture & Technology Portfolio
We deliver end-to-end solutions for construction site automation—covering everything from electrification and remote control of machinery to autonomous operation software and full-site visualization and management tools.
Our flexible, modular technologies can be tailored to match the unique demands of each job site, helping you accelerate productivity and unlock smarter operations.
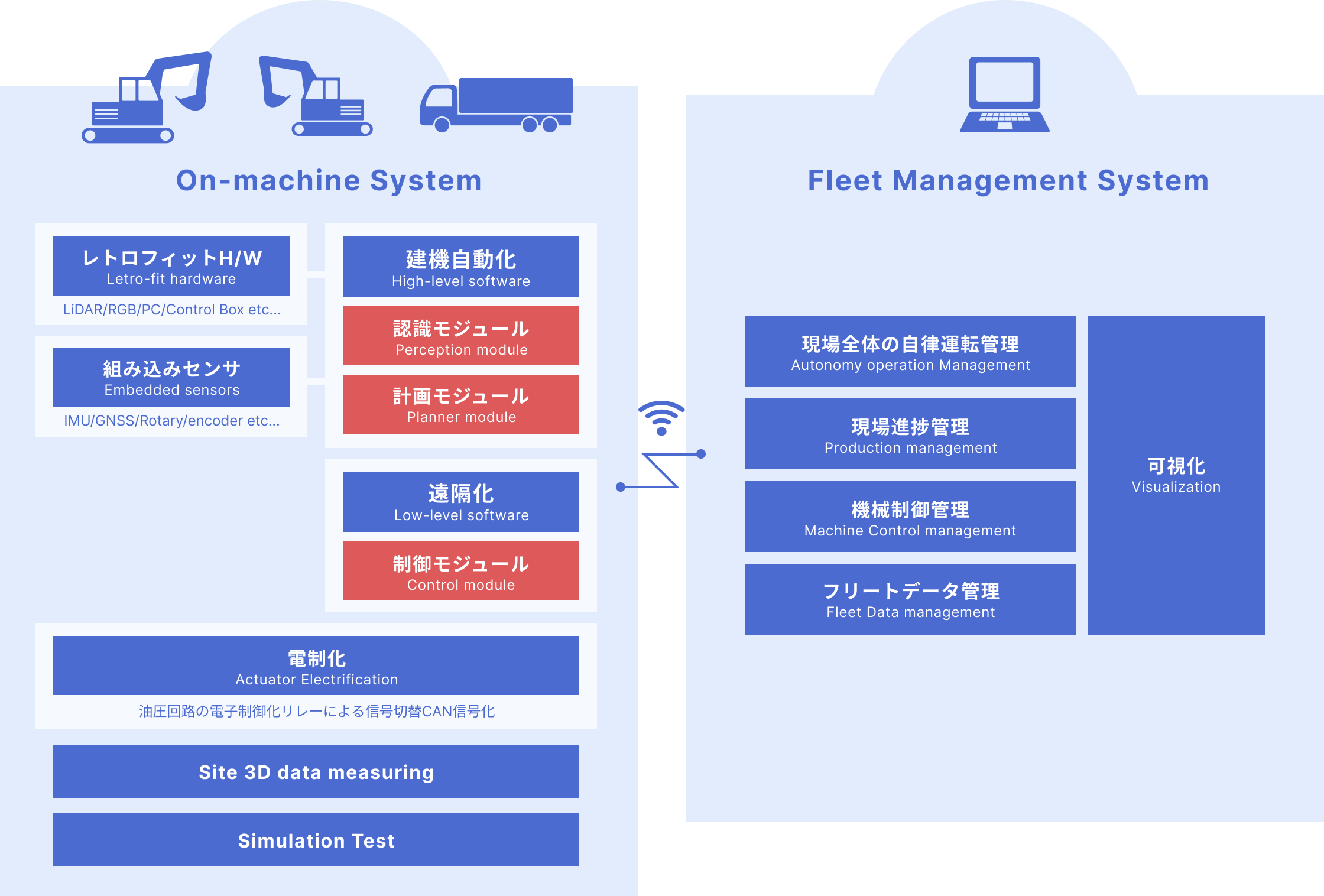
Our Development Process
We start by understanding your challenges and analyzing your specific needs.
From there, we develop tailored solutions step by step—with a clear focus on practical, real-world implementation at your job site.
-
1
Requirement
Analysis・
Solution Proposal -
2
Electrification of
Construction
Machine -
3
Functional
Development -
4
Development of
Automation
Systems -
5
Operations and
Maintenance
Development Flow
We adopt a hybrid model combining the V-Model and Agile methodologies to address the technical challenges and uncertainties in development.
-
In traditional V-model development, the entire system is carefully defined upfront through detailed requirements analysis. All features are planned in advance, and development proceeds step by step from the top down. However, it’s not uncommon for this process to take over a year before the customer can actually test the system in the real world. When that time finally comes, it’s often the case that missing requirements or new feature requests emerge—creating costly delays and rework.
Typical
Software Vendor -
At DeepX, we take a more agile and practical approach. Instead of waiting a year for results, we complete an initial V-model development cycle in just 2–3 months—allowing basic system functions to be tested on actual machines early on. From there, we repeat shorter V-model cycles in an agile style, incorporating additional requirements and verifying real-world performance at each step. This enables us to deliver the system you need, faster and with greater flexibility. We also provide a simulated environment that mirrors the real work site, making it possible to test each function in advance. Even before field deployment, we can run validation cycles every 2–3 weeks—reducing risk and accelerating implementation.
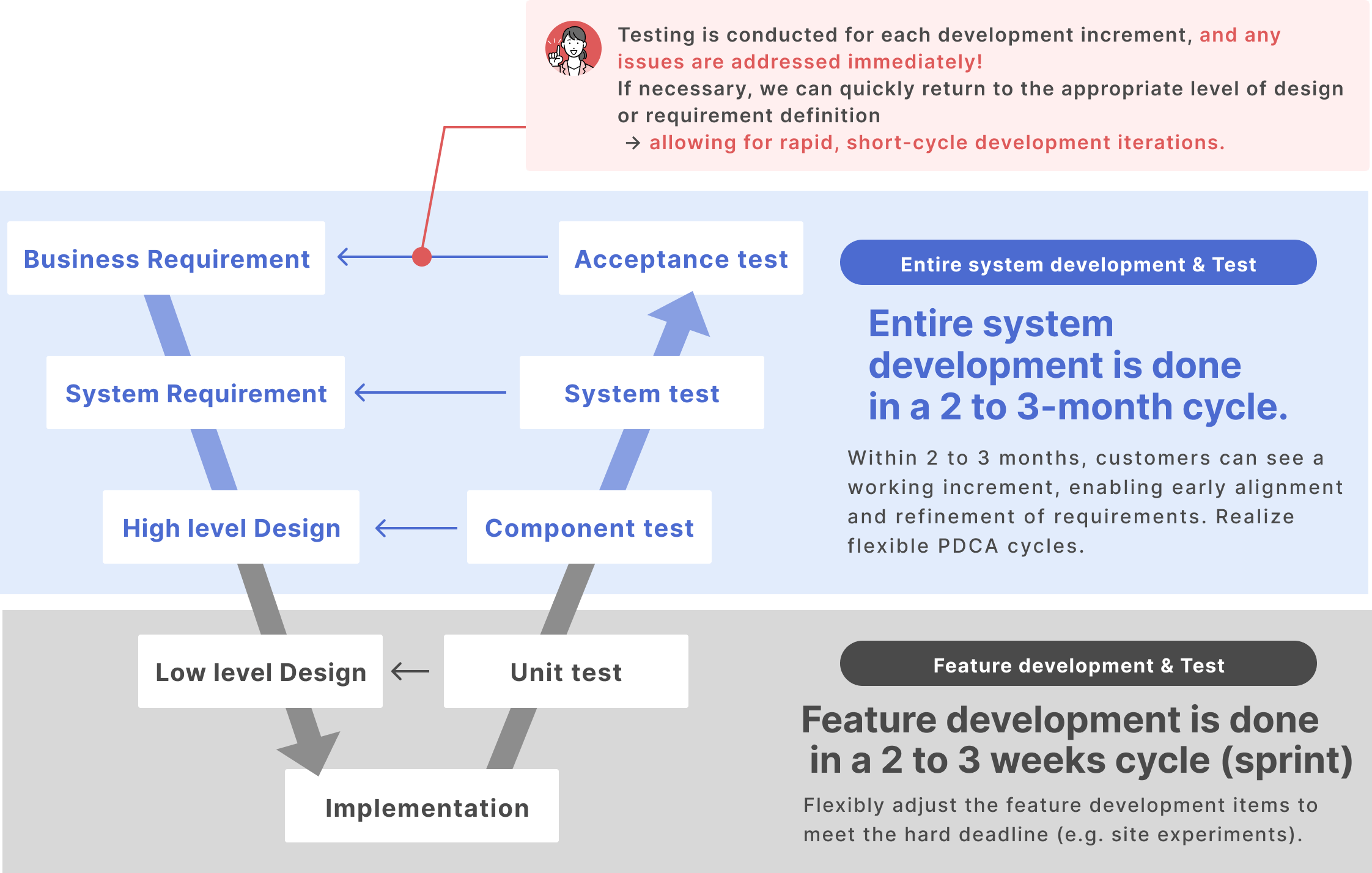
Contact
If you have any inquiries or would like to discuss your project, feel free to reach out.