DeepXは、油圧ショベル自動運転システムを開発し、2023年4月、株式会社フジタ(以下、フジタ)とともに、掘削からダンプ積み込みを一作業とする一連の繰り返し操作の自動運転を、造成現場で実証しました。
建設現場での自動運転の実現には、複雑なシステムの安定化が必須
周辺環境や対象物に応じ自律的に動作するシステムは複雑であり、自動運転システムを含むそうしたシステムの連続的かつ安定的な動作には課題がありました。
例えば、実際の建設現場では、油圧ショベルに対してダンプの条件を1つに固定することは難しく、積み込み時には、油圧ショベルの周辺を認識し、ダンプの位置や姿勢、ベッセル内の土の量や形状など、複雑な条件に応じて柔軟に動き分ける必要があります。また、掘削対象である土の形状や硬さも状況によって多様であり、掘削時にはそれらの多様な条件に応じてリアルタイムに動き分ける必要があります。一方で、一般的にシステムが対応する条件が複雑になればなるほど、システムの安定性は損なわれる傾向にあります。
実用化に向けて必須な要素である安定性を維持しつつ、複雑な条件に対応するシステムの実現には課題がありました。
掘削・積み込みの繰り返し連続作業の自律化を現場で実証
本実証では、フジタの造成現場にて、掘削からダンプ積み込みの一連の繰り返し作業を対象とし、操作の自律化を実現させました。作業内容としては、ダンプトラック(位置や姿勢、ベッセル内の土量等)に応じた油圧ショベルの自律的な動き分けができること、及び、一定の範囲で指定された掘削対象領域の土の形状や残留土量に応じた油圧ショベルの自律的な動き分けができること、を確認しました。また、システムの安定性として、約8時間にわたり連続で稼働し、合計で200回以上の掘削と積み込みを1日でできることを確認しました。
ROS2をベースに、油圧ショベル自動運転システムを構築
DeepXは、主に、ソフトウェアの開発や提供、それらを利用した現場でのインテグレーション業務を担いました。ソフトウェアについては、ベースとなるロボットシステムに加えて、認識や制御のアルゴリズム、開発検証のためのシミュレータを開発しました。その他、実証実験に必要な実証現場やハードウェアの手配等は、フジタが対応くださいました。
開発した主要なソフトウェア
ロボットシステム
ROS2をベースとしたロボットシステムを開発しました。本実証では、本実証の後に実運用を見据えており、そのため、特に、システムの頑健性および拡張性を重視した開発を実施しました。
ダンプ認識
Lidarからの点群データを処理し、油圧ショベルから見たダンプの相対的な位置や姿勢、ベッセルの形状、積み込み状況等をリアルタイムに把握するシステムを開発しました。特に、さまざまな位置や姿勢、土形状などの条件に対応できるようにするために、ディープニューラルネットワークを活用しアルゴリズム開発を行いました。
掘削パス生成
土の形状に応じて掘削軌道を自動で生成するシステムを開発しました。本実証では、土の形状に応じて、浅く掘ったり、深く掘ったり、掘る場所を変えたりと、適切な動き分けができることを確認しました。
開発組織
本実証では、顧客と密にコミュニケーションし開発の要件定義や実証を推進するソリューションチームと自動運転システムを開発するソフトウェアエンジニアチームが連携し、ソフトウェアの開発と実証を行いました。特にソフトウェアエンジニアチームは多くのメンバーが外国籍でありグローバルなチームとなっています。
現場での実証実験に従事する外国籍のエンジニアメンバー。
今後の展望
今回開発したソフトウェアをベースに、大規模造成現場での実作業の自動運転の実証に向けて動くことを予定しています。
今後も引き続き建機自動運転の実用化に向けたフロンティアを開拓していきます。
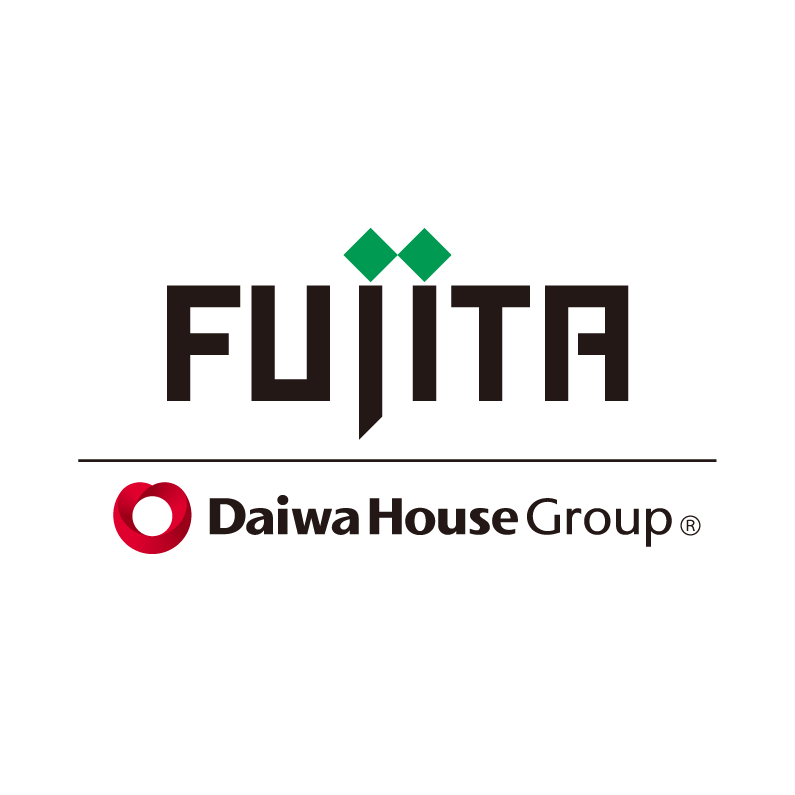
株式会社フジタ
https://www.fujita.co.jp/1910年創業の総合建設会社。高い技術力と提案力で、国内のほか、中南米やアジア圏等で数多くの施工実績を積み重ねている。国内外で培ってきた建設技術ノウハウや技術イノベーションによる新規事業の創造に大和ハウスグループの総合力を加え、お客さまに新しい価値を提供している。